Simulation Integrated Manufacturing
SIM Cyber Physical Production Concept of IoT era “Simulation Integrated Manufacturing (SIM)”
SIM is the concept to innovate toward Manufacturing of IoT era.
By IoT and Artificial Intelligent Technique, Production Activity will be optimized and Cyber Physical Production will be promoted.
Why and for what purpose “Simulation Integrated Manufacturing” is required?
In the times of globalization to cope with the drastically and rapidly changing world of business, transition to a new manufacturing concept is required. With IoT in rapid progress, production innovation efforts that take the regional industrial cultures into consideration are underway overseas, such as the “horizontal division of work” in the Industry 4.0 framework in Germany and the “highvalueadded services” approach adopted by GE and other players in US.
However, just smart machine concept from Indstrie4.0 does not give you the practical production system and a future of manufacturing. To move the manufacturing innovation forward, what we should try to do now is not to follow implementing IoT but to leverage and maximize the inherent strengths with “vertical integration approach”.
This strength can be enhanced through latest technologies to develop a “predictive engineering” approach, where problems can be foreseen and coped with before they even occur and changes and new trends can be predicted and dealt with in an effective manner. “Predictive engineering” refers to an upstream engineering approach where potential issues and problems are exhaustively identified and coped with in the production system planning stages. With this, the best possible performance and quality can be assured in the planning stage.
This is a next generation manufacturing concept where ICT (information and communication technologies), IoT and the manufacturing strength are united into one.
How “simulation integrated production” actually works
LEXER RESEARCH Inc. is currently promoting a new manufacturing concept called “Simulation Integrated Manufacturing (SIM)”, that enhances engineering operations from organizational aspects through predictive engineering techniques. SIM enables stronger coordination of upstream operations through production simulation and also drastically improves production management by bringing IoT features to the production floor. Furthermore, SIM fully transforms engineering operations by replacing the conventional type of scattered operation structure with a more centralized and closely coordinated one.
SIM is mainly implemented in two operational areas; the upstream operations up to the start of mass production and the downstream operations subsequent to it. What to do in each of these areas is briefly described by the following objectives:
- Vertical integration of production engineering operations
- Dynamically optimized production with massively parallel simulation system
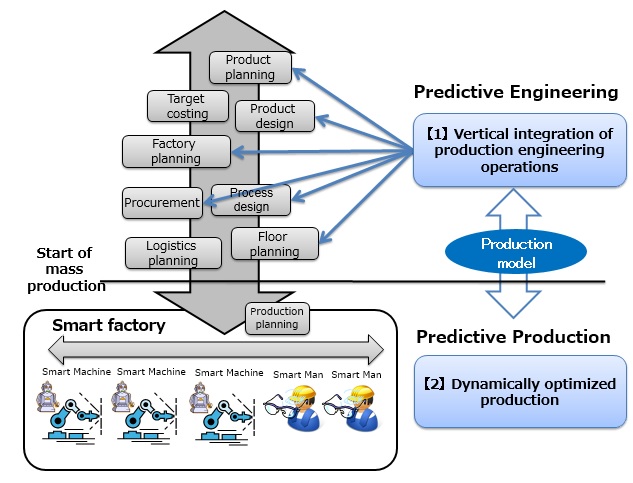
The actual steps to achieve the two objectives are explained in the following paragraphs.
1. Vertical integration of production engineering operations
Upstream operations to manufacture a product start from project level planning activities including product planning, factory strategy planning and target costing, followed by more practical planning and design activities including product design, process design, procurement and line planning, to prepare and provide all that is necessary to start the mass production of the product. By configuring these activities based on a common production system concept, they can be organically linked within a single production model framework.
Furthermore, the tangible elements of production, such as the product and parts, equipment, tooling and layout, and the intangible elements such as the work and process, transportation, logistics and production plans, can be put together through production simulation to assess if the relationship between the elements is practical and feasible.
To achieve the vertical integration of production engineering operations, various planning services can be configured and evaluated in individual operation processes to determine their feasibility and effectiveness, so that upstream operations can be made more efficient and more effectively organized. This is a new engineering approach that shifts from the conventional fragmentary optimization attempts toward a more comprehensive and business processintegrated optimization. In addition, extensive use of IoT features will enable creating a production plant database called “global factory repository” that can fully synchronize with the actual production environment to facilitate production engineering activities.
Vertical integration of production engineering operations
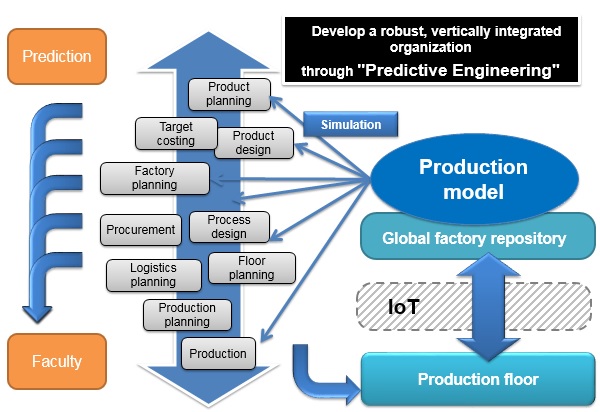
Now, what do all of these steps mean and in what respects are they different from the conventional approach?
A) Under the conventional system, there has been no clearly defined operation process management spanning multiple organizational sections, and as a result there used to be a lot of going back to the previous process for correction before moving forward. With the predictive engineering approach, there will be no more such “going back for correction” as all potential issues are exhaustively identified and dealt with in advance.
B) Production models that are created through conventional data sharing techniques such as ERP and PLM are too rigid and abstract and therefore cannot cover all the preproduction engineering operations with an adequate level of detail or precision. However, the combination of multiscaling techniques and a management structure designed for circulative implementation will allow the production models to be more flexible and more adaptive to a wider range of operations.
C) Conventional production models used to be too abstract and too distant from the actual production environment due to insufficient input of physical information. Production models that more accurately represent the actual situation, added with massive use of IoT features, will enable more effective synchronization with the production environment so that what really goes on on the production floor will be truly reflected in planning activities.
D) Expert knowledge used to exist within specific individuals only and therefore was not obtainable except through onhand activities on the production floor. By integrating those individually owned yet truly effective and proven experience and knowledge into production models will make such knowledge available for and usable by everybody else n the organization.
To realize all of the above, it is not enough to merely make more production models and improve functionality. We must go one step further, to create production models that truly represent the actual production conditions and to establish a system where expert knowledge is contained as a thoroughly systematized set of methodology. This should be the basis of all engineering operations, and that is what “vertical integration of production engineering operations” is all about.
2. Dynamically optimized production with massively parallelsimulation system
Once the mass production of a product commences, it is typically very common that unexpected issues and problems such as machine failures, quality defects or emergency orders are experienced as a everyday occurrence. You would be required to resolve all such issues quickly to recover normal production state as soon as possible. Such process of problem solving and recovery is called “resilience”, which, unfortunately, often does not occur very easily in a production operation. Once production deviates from the established schedule, recovery can be difficult and timeconsuming.
A “dynamically optimized production system”, when faced with a problem such as an equipment failure (serious or minor), emergency production order, nondelivery of parts or quality defect, immediately runs real time simulation to assess how serious the situation is and how it impacts the production. An optimization process will then start that, by executing massively parallel simulation, identifies and executes all possible remedies and improvements such as modifying the production plan, changing the production line allocation or adjusting the workforce plan, so as to autonomously seek recovery or otherwise control the situation as best as possible. In short, a dynamically optimized production system enables you to effectively cope with variations, disruptions and turbulences experienced in a production operation through active use of production simulation techniques.
To put a SIM concept into practice, it is necessary that IoT features are available for use. On a human operated type production line, a cyberphysical system is employed to monitor the work instructions received and the work performances recorded to assure that production continues without problems. On the other hand, an MES or smart machine will be utilized on a machinedriven type production line to retrieve work performance data while production continues. If a work delay is detected, the massively parallel simulation system will run dynamic optimization in an intermittent manner, monitoring and correcting the production plan and the production system as required to resolve the delay to maintain normal operation.
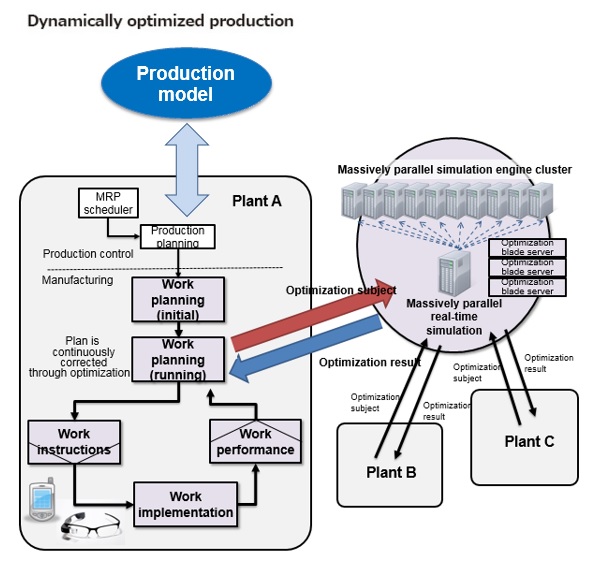
Finally, what role SIM is to play in a manufacturing organization as a whole? SIM can be implemented in a mutually complementary manner to other manufacturing systems such as PLM, ERP and MES. Presently, systems such as PLM, ERP and MES each work as a “closed loop”, but SIM can make all of these systems linked and coordinated to create an environment that allows more comprehensive engineering implementation, and production models can work as a hub at the center of such environment to constitute an organic linkage between the systems.
Role of “Simulation Integrated Manufacturing” in a manufacturing organization
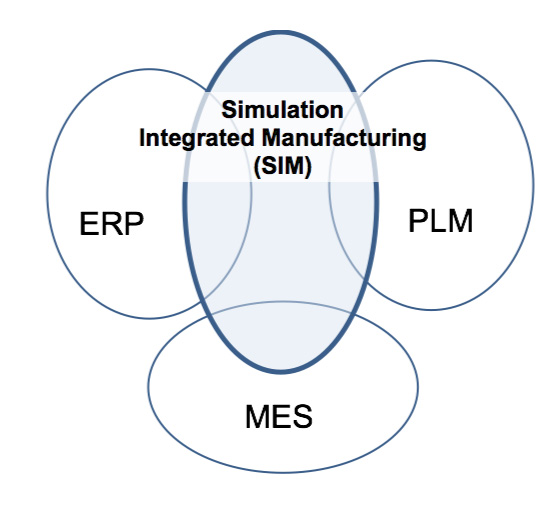